Speaker interviews: Compounding World Expo North America
15 October 2024
Excitement is building with less than one month left until we open our doors to the Compounding World Expo in Cleveland!
We have been busy collecting interviews with our esteemed speakers for the free-to-attend conference sessions, which will feature technical talks, industry debates, and market forecasts.
The full interviews are available to read here, but here’s a quick preview:
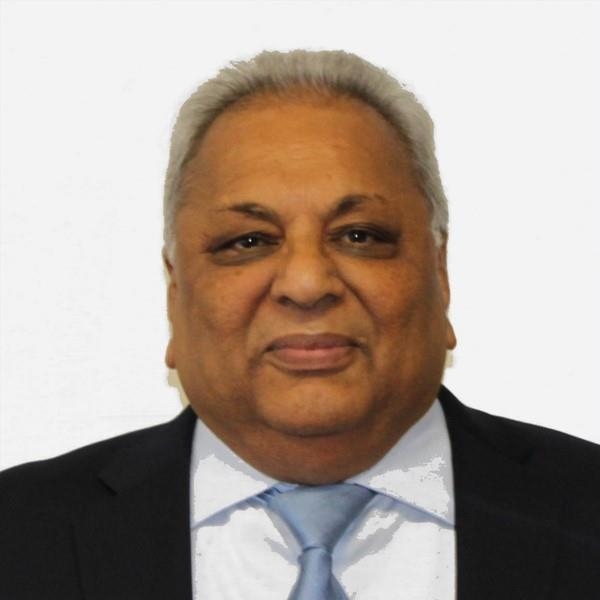
Mike Patel, Teknor Apex
Mike, having worked at Teknor Apex for over 20 years, what have been the accomplishments you’re most proud of?
Leading the expansion of LS FRPVC FireGUARD and launching of LS HFFR HalGuard product lines, both of which have made significant contributions to the growth of the business are some of the accomplishments that have given me personal satisfaction.
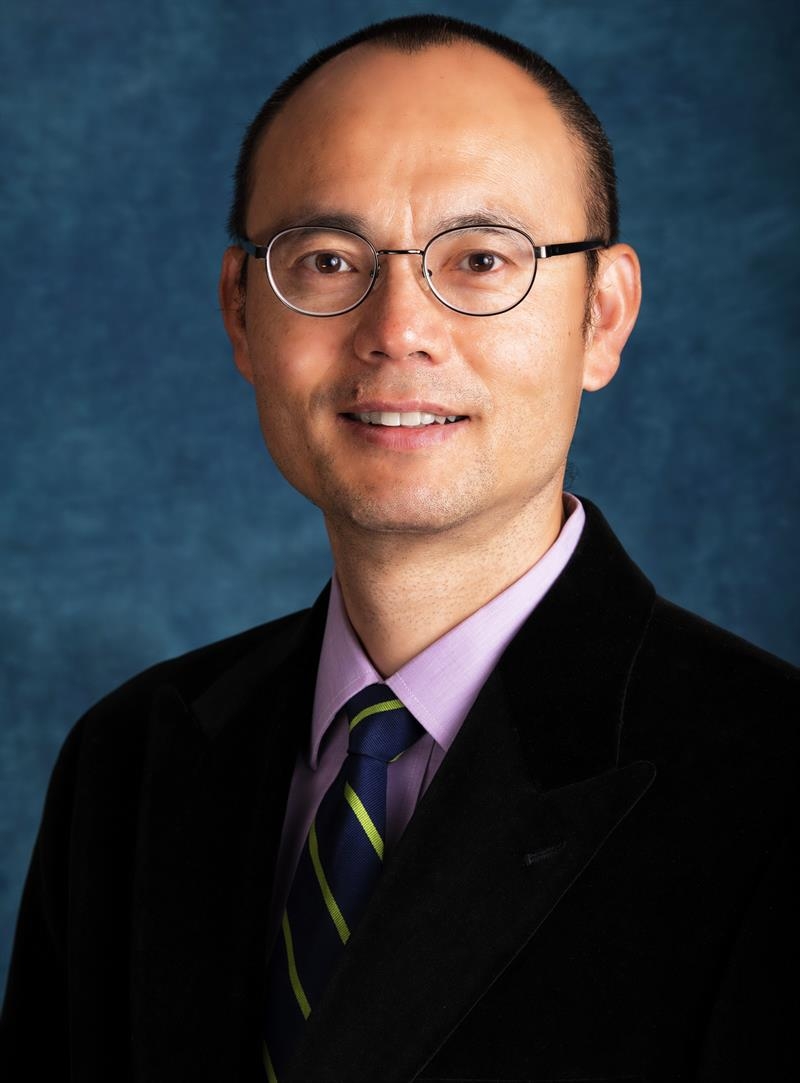
Dr. Peng Ye, Farrel Pomini
Dr. Peng, what are the common challenges of PHA compounding?
PHA, like other biodegradable plastics, present several processing challenges. It is temperature and shear sensitive, susceptible to moisture build-up as well as molecular weight loss and material degradation.
Farrel Continuous Mixing technology is extremely well-suited to address these challenges. We had the benefit of conducting studies in partnership with CJ Biomaterials. The research clearly demonstrated that the Farrel Continuous Mixer outperformed the twin screw extruder on many process parameters.
The specifics will be detailed in our presentation Wednesday, November 13 at 10:10 in the Compounding Theater.
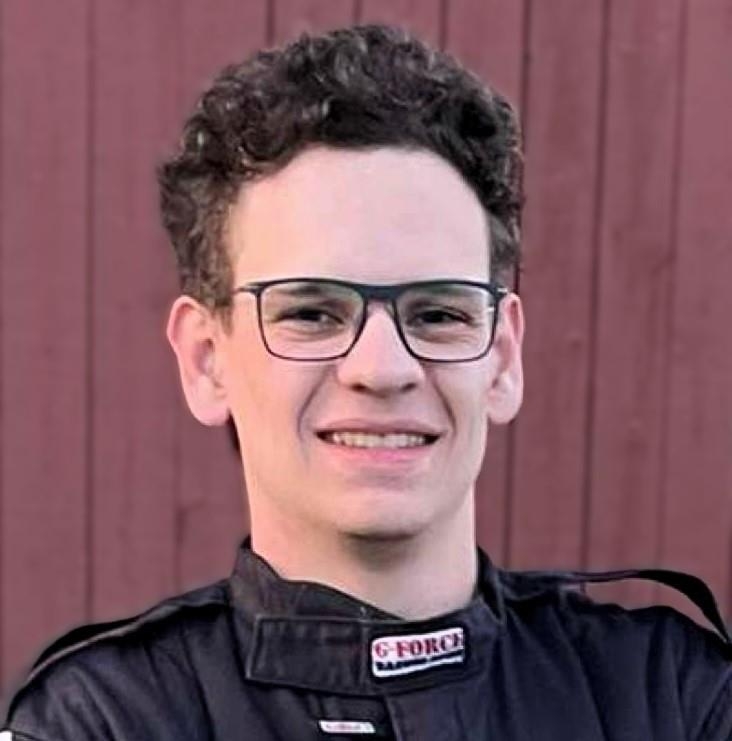
Onur Ege Onar, Mine Colours
Onur, how do you work towards achieving greater sustainability?
Sustainability is a core value at Mine Colours. As a European-based company, we're well-positioned to stay at the forefront of environmentally conscious practices, especially given the increasingly stringent regulations around plastics.
We offer a range of more sustainable products at different price points, giving our customers the option to incorporate Post-Consumer Resin into their colorants. While using recycled resin presents unique challenges - especially in color matching due to the variability of the material - we are committed to overcoming these hurdles. We view it as our environmental responsibility to reduce plastic waste and contribute to a greener future.
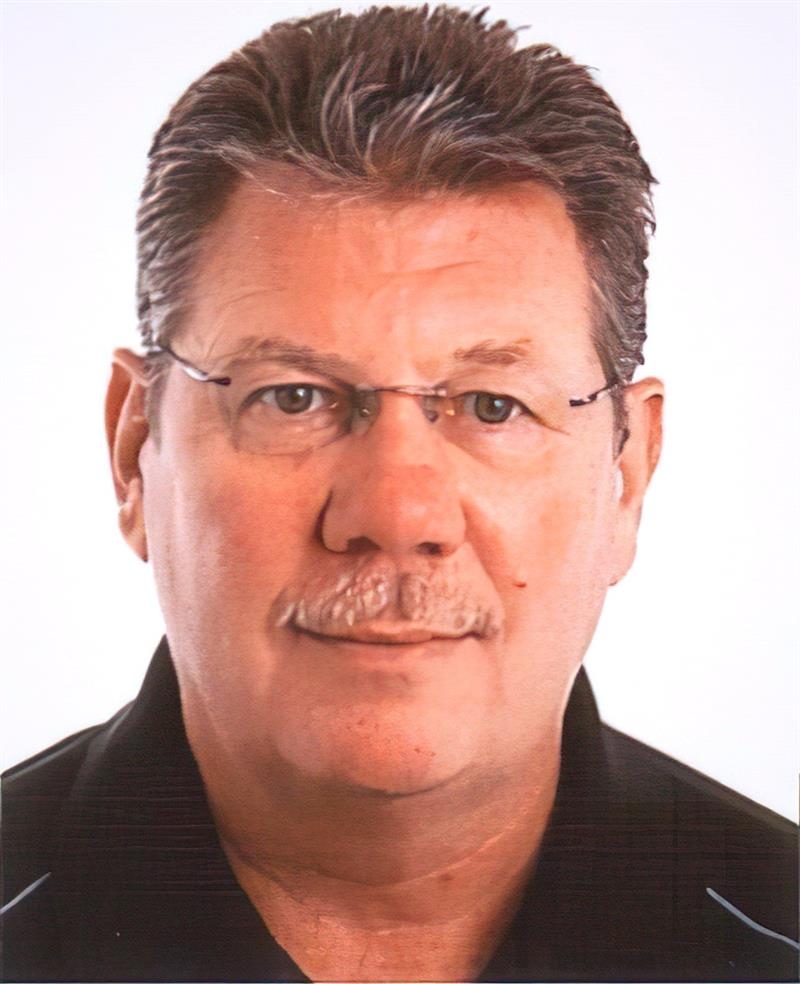
Michael Batton, ENTEX
Michael, what are the main challenges you hear from customers?
Customers primarily want to reduce processing costs in all areas. Developing and implementing extrusion lines to meet the demands of today. To include material temperature control, heating and cooling on the same central screw, high levels of de-volitation, wide processing tolerances, and continuous processing are all part of the requirements on machine manufactures today. Sustainability also plays a big role in the demands of today.
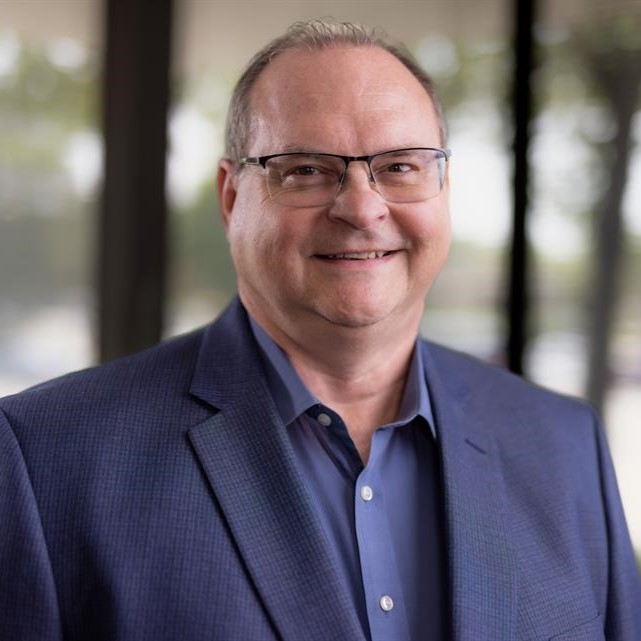
Todd Baker, Horizon Systems
Todd, how do you best define innovation?
Our approach to innovation centers around identifying your specific challenges and then developing mutually beneficial solutions. We employ customized approaches, incorporating innovative ideas, processes, and solutions to enhance our customers' productivity and profitability.
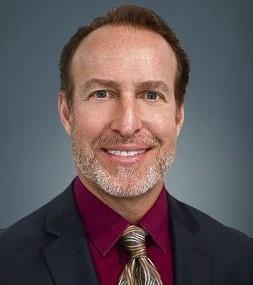
Douglas Brownfield, Ampacet
Douglas, with AI being an important talking point at the moment, can you explain how it operates within color measuring?
Today’s sustainability objectives require increase usage of PCR and PIR resins. These recycled materials present significant challenges for plastic processors when it comes to maintaining consistent color standards.
PCR and PIR resins often fluctuate in color consistency, even within the same batch, leading to costly downtime and scrap for processors as they work to correct off-color issues. In addition, the ongoing shortage of skilled labor makes it even more challenging and expensive to maintain high production quality. AI technologies, like the new SpectroMetric 6 in-line color measurement and correction system, create a closed-loop quality control system that enables extrusion companies to achieve consistent color quality - even when using recycled resins - without the need for operator intervention.
The patented, Spectro fiber optic sensor continuously measures the color of the extruded material in real-time and calculates deviations from the set color standard. The AI SpectroMetric software then determines which pigments are required to adjust the color’s L.a.b. values. The SpectroMetric then micro doses appropriate ratios of mono pigments to the resin blend at the extruder. This AI technology eliminates the need to shutdown the line to make the appropriate adjustments after the line operator or QC manager determines the proper changes in color required. Today, most line operators simply increase the percentage of color to off-set the color deviation, but this significantly increases the cost of color for the company, and color is already is expensive.
Additional interviews are availbale with:
- Tribu Persaud, Norwich Plastics
- Ralph Purtell, Purtell Vinyl Consulting
- Dr. Lifeng Chen, US Silica
- Herwin Santos, Lindor
- Carolyn Pressley, Budenheim
- Tom Inch, BYK USA
- Dr. John Swanson, NeoGraf Solutions
Take a closer look here