Covid-19 pandemic impacts the supply chain for wind turbine blades in 2020 after an exceptional growth phase between 2017-2019
12 June 2020
AMI Consulting estimates that global demand for materials (in weight) for the production of wind turbine blades grew at an average rate of 12.5% p.a. between 2017 and 2019. Demand growth has been particularly strong in Asia and North America. The "PTC bubble" in the US and China's 13th Five Year Plan on Energy Development (2016-2020) are the two main drivers for the fast growth seen between 2017 and 2019. In turn, this has made 2020 a critical year for both China and the US, the two largest wind energy markets in the world.
The industry had anticipated blade production to reach a peak in 2020, all driven by government incentives. The COVID-19 pandemic is having a clear impact on the wind turbine blades supply chain in this critical year.
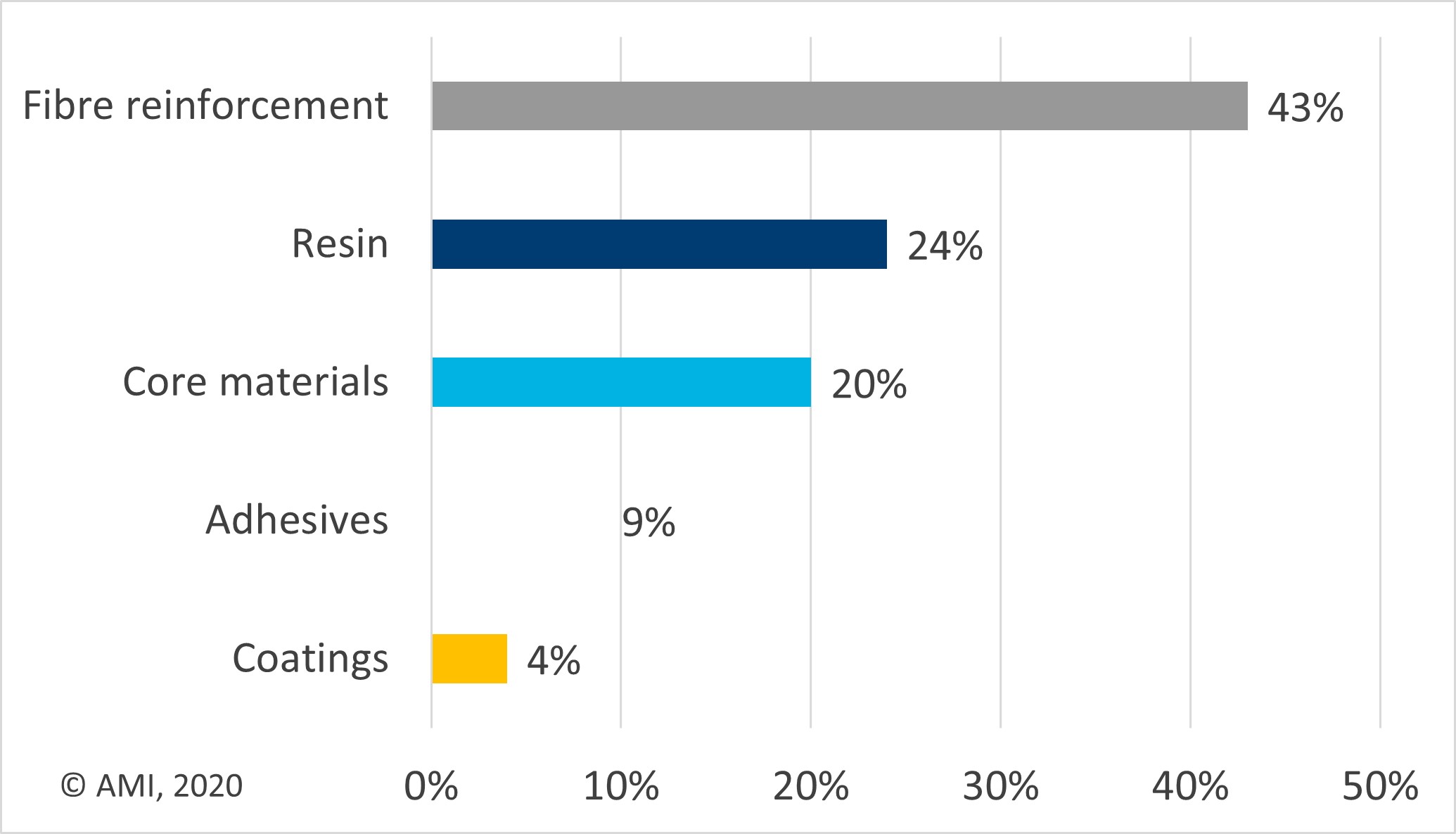
Approximate global market sales value by material in 2019
AMI Consulting estimates that global demand for materials (in weight) for the production of wind turbine blades grew at an average rate of 12.5% p.a. between 2017 and 2019. Demand growth has been particularly strong in Asia and North America. The “PTC bubble” in the US and China’s 13th Five Year Plan on Energy Development (2016-2020) are the two main drivers for the fast growth seen between 2017 and 2019. In turn this has made 2020 a critical year for both China and the US, the two largest wind energy markets in the world.
The industry had anticipated blade production to reach a peak in 2020, all driven by government incentives. The COVID-19 pandemic is having a clear impact on the wind turbine blades supply chain in this critical year. An overview of the consequences of the pandemic are covered in AMI Consulting’s report, reflecting the experiences of leading players in the industry gathered through exhaustive research.
The industry continues its transition towards energy auction systems, a process that in some countries has not been a smooth experience. With the move towards auction systems, the need for manufacturers to maintain low cost of energy levels is more important than ever. The increased competition among wind turbine manufacturers continues to exert pressure on prices. The report provides a comprehensive review of the different commercial strategies adopted by OEMs and raw material suppliers to adapt to this competitive pressure.
Increased effort is being invested into blade designs to maximise power generation and reliability while minimising weight. This requires careful attention to materials, processing and blade design. To maximise generators’ return on investment, average blade size is getting longer. As blade length and weight grow, increased sophistication in blade design, materials and manufacture are required. The link between generating capacity and blade size is examined in the report. Increasing blade length has not only been driven by offshore wind energy growth but also to maximise wind capture of onshore wind turbines on low wind speed sites, specified at a lower power rating.
The production of longer blades is having a significant effect on material consumption for blade production both in terms of quantity and quality, accelerating demand for higher performance materials. At the same time, certain materials have been commoditised. The different market dynamics within each material group have brought very interesting material selection trends, not only around fibre reinforcement (where carbon fibre consumption increases), but also in other less obvious areas including core, adhesives or coatings. These trends have affected material suppliers’ market share as detailed in the report for each material, together with a comprehensive assessment of the pros and cons of the material alternatives available alongside a review of the material shortages experienced by the industry.
As wind turbines get larger and technical standards rise, so the financial bar is raised for blade manufacturers to compete leading to further market concentration. The wind turbine blades market has changed significantly in recent years as a result of this consolidation process that has reduced the number of players to the point that, during 2019, the top five blade manufacturers accounted for almost 60% of material demand by weight. This clear and addressable market volume makes it a very attractive market for material suppliers, even for commoditised materials, given the scale of these accounts. Consolidation has affected both onshore and offshore markets, but the onshore market continues to be significantly more fragmented than offshore.
Regionally, market consolidation has particularly affected Europe, where AMI Consulting has identified the highest number of changes on blade production operations. However, Europe maintains technological leadership in this market. This is particularly relevant for offshore, which is expected to be one of the most important factors driving growth over the next few years. China’s position in the global industry is significant but can be hard to quantify. AMI Consulting has invested significant time and resources on understanding this region, bringing clarity in order to help subscribers gain critical insight into this key region.
The wind turbine blades industry is not an exception to the global growing awareness around sustainability, which has driven companies like Vestas to set ambitious sustainability targets. AMI Consulting has investigated the impact that this kind of targets have on material suppliers, including for the first time in this report, information raw material suppliers should bear in mind in relation to circular economy, carbon footprint and toxicity.
By providing independent qualitative and quantitative analysis, subscribers will gain a strong understanding of the scale of the market, its dynamics and the changing market share of the key participants.
Highlights of the report Material Usage in Wind Turbine Blades – The Global Market 2020:
- Market size and growth of each material used in wind blade manufacture, segmented by sub-types of fibre reinforcement, resins, core materials, adhesives and coatings (including LEP)
- Detailed material consumption for each blade manufacturer, by type of material and by region
- Size and positioning of the main wind turbine blade manufacturers (by material consumption)
- Size and positioning of the main material suppliers (by volumes sold during 2019)
- Analysis of the status of the blade technology, manufacturing materials and inter-material substitution trends
- Data provided for the years 2014, 2017, and 2019 and forecasts for 2020 and 2024.
Take a look at the latest market research from AMI here